Mass finishing is increasingly becoming the best way to finish components confining hand finishing to the history books. Vibratory finishing is a mass finishing process used to burnish, deburr, clean, radius, de-flash, remove rust, brighten, surface harden, surface improve and edge break.
Mass finishing is increasingly becoming the best way to finish components confining hand finishing to the history books.
Vibratory finishing is a mass finishing process used to burnish, deburr, clean, radius, de-flash, remove rust, brighten, surface harden, surface improve and edge break.
Whether the finishing machine is vibratory, barrel or centrifugal the finish of the final component will be of a higher quality and consistent. Removing the possibility of human error is means fewer rejects. Another advantage is that the machines can run 24/7 creating far higher capacity.
From a purely business perspective deburring using a deburring machine makes complete sense. Deburring equipment does not have to cost the earth. If you source your machine from a reputable and trustworthy supplier you’ll never look back.
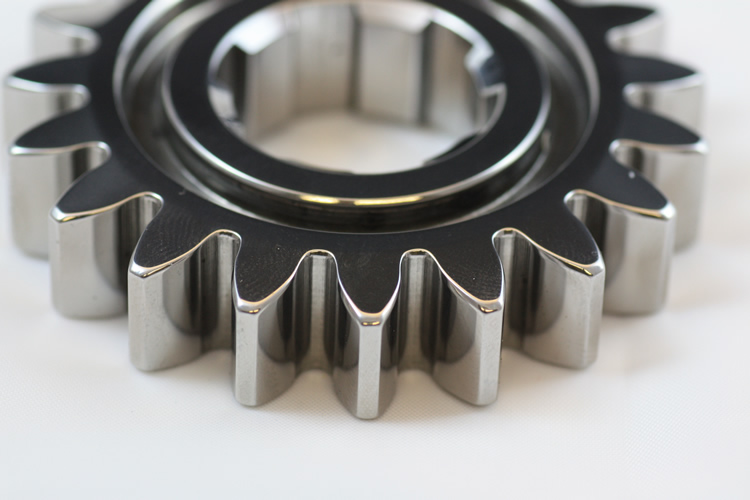
Mass finishing machines come in all shapes and sizes and should be selected depending on what job it will be expected to do.
Vibratory deburring: Vibratory mass finishing machines are essentially motorised process chambers mounted on springs. The components and media held in the chamber oscillate and rotate in a toroidal (corkscrew) movement. The surfaces of the components are agitated much like pebbles on a beach. The result is the removal of burrs and a consistent polished finish. Fragile parts can be deburred in this way as the constant moving of the components and media means parts are not damaged.
Barrel deburring: reduces surface irregularities to produce a clean, smooth surface. It achieves this by tumbling the parts against themselves or additional media such as steel balls. It is also usual to add water and a cleaning agent. Vibratory tumblers offer an aggressive form of deburring that is ideal for parts that require a significant radius. Components need to be robust as part on part damage can occur. It is not suitable for CNC milled components or pre-anodised finishing.
Centrifugal deburring: is an enhanced “barrel” deburring process. A disc within the chamber is rotated adding centrifugal forces to the process, which in turn speeds up the polishing process by 25 to 50 times that of barrel finishing machines. Centrifugal disc finishers require a constant flow of water and chemical additives to ensure the required finish is achieved.
As technology advances, more and more tiny/fragile components are being manufactured. If these small parts are robust, like coin blanks, centrifugal finishing may be a better alternative to the standard vibratory machine.
The centrifugal disc machines have the added advantage over centrifugal barrel machines (planetary finishers) of being open. This allows the heat generated by the process to escape. Centrifugal barrel finishers need to be periodically shut down to allow the built of pressure to be relieved. This downtime is avoided with the centrifugal disc machines.
The media also needs to be right
The success of all these mass finishing options rely on the correct use of media. Media vary in terms of size, shape, weight & material. Ceramic media are heavy and abrasive, plastic media are lighter, smooth and long lasting. Porcelain media are expensive but achieve low Ra finishes. The point being that expertise is crucial when it comes not only to buying the right mass finishing machine but also when it comes to selecting the right consumables.
Find a supplier that will undertake production quality testing before they recommend which mass finishing machine you need. Ask that their recommendation includes the specification of the media you will need as well as processing times.