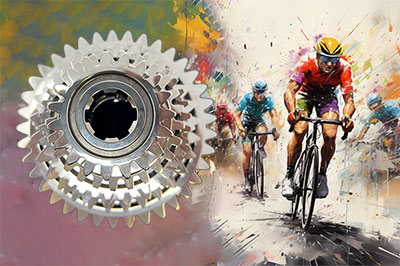
Vibratory finishing is a versatile process that effectively handles a variety of tasks for individual components or stillages. It's an efficient method that costs approximately £1 per hour, making it a cost-effective choice for many applications.
The process begins with degreasing, where the vibratory finishing method effectively removes grease from the components, ensuring a clean surface for the subsequent steps. This is followed by a thorough cleaning process that eliminates any remaining dirt or impurities.
Next, the vibratory finishing process deburrs the components. This means it removes any rough edges or 'burrs' that may have been left behind from the manufacturing process. This is crucial for ensuring the safety and functionality of the components.
In addition to deburring, vibratory finishing also performs edge breaking. This process smoothens the sharp edges of the components, improving their overall appearance and making them safer to handle.
The surface improvement phase follows, where the vibratory finishing process enhances the surface quality of the components. This step ensures the components have a consistent and smooth surface, which is often necessary for their intended use.
Polishing is the next step in the vibratory finishing process. This step gives the components a shiny, smooth finish, enhancing their aesthetic appeal.
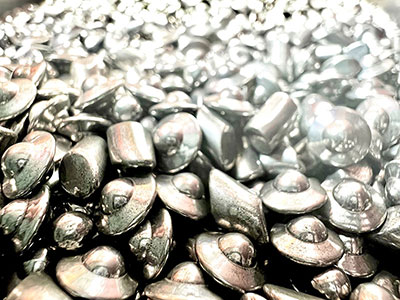
Finally, the vibratory finishing process concludes with super finishing. This is the final touch that ensures the components have a high-quality, professional finish. This step can significantly improve the component's resistance to wear and corrosion, extending its lifespan.
In summary, vibratory finishing is a comprehensive and cost-effective process that degreases, cleans, deburrs, edge breaks, improves surfaces, polishes, and super finishes components or stillages, all at a running cost of about £1 per hour.